Технологии
ЛЕТАТЕЛЬНЫМ АППАРАТАМ - ВЫСОКОПРОЧНЫЕ СТАЛИ
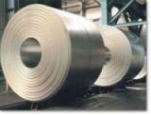
Условия эксплуатации современной авиационной и космической техники предопределяют крайне жесткие требования к материалам, из которых ее изготавливают.
Здесь и необходимость достижения высокой прочности конструкции при минимальном удельном весе, габаритах и расходе топлива; обеспечение достаточной надежности и длительного рабочего ресурса при воздействии переменных и значительных силовых нагрузок, чередовании повышенных (до 450 градусов) и пониженных (до -253 градусов) температур, коррозионно-активных сред, различного рода излучений и др.
От качества материала в значительной степени зависит конкурентоспособность летательных аппаратов. Для военной техники важны такие характеристики, как дальность полета, скорость, маневренность, точность, возможность полета в любую погоду, грузоподъемность, обеспеченность производства отечественным сырьем; для гражданской - надежность, пожаробезопасность, комфортность, экологичность и т.д. Причем всего этого нужно добиваться при минимизации затрат на разработку, освоение и эксплуатацию машин.
Из перечисленного ясно: используемые в самолетостроении материалы должны обладать высокой удельной прочностью (ее еще называют весовой эффективностью) и жесткостью, коррозионной стойкостью, сопротивлением усталости , а также трещиностойкостью и рядом других. Конечно, обеспечить все требования один какой-то материал просто не в состоянии, поэтому при изготовлении различных частей летательных аппаратов используют самые подходящие из существующих, или создают новые композиции.
Наибольшее применение в настоящее время нашли алюминиевые сплавы. Из них изготавливают нижние и верхние поверхности крыла и фюзеляжа (здесь необходима прочность в пределах 450-550 МПа), элементы так называемого силового набора - различные ребра жесткости и связующие их шпангоуты, фитинги, балки с пределом прочности 500-600 МПа и т.п. Доля таких материалов в современных самолетах доходит до 50-70%.
Весьма распространены титановые сплавы (из них делают отдельные детали шасси, различные балки и др.) и, особенно, полимерные композиты. Последние применяют для изготовления панелей крыла, горизонтального и вертикального оперения, створок люков шасси и силовых установок. При прочности 1700-2500 МПа они имеют удельную массу менее 2 г/см 3 . Их доля в самолетах составляет 8-15, а в вертолетах - около 50%.
На первый взгляд, казалось бы, что в столь представительной "компании" роль сталей должна снижаться, однако дело обстоит совсем иначе. На их долю в пассажирских лайнерах приходится 8-10, в военных - 25 - 50%, и в ближайшем будущем такое соотношение по крайней мере не уменьшится. Стальными делают наиболее нагруженные элементы летательных аппаратов - детали шасси, корпуса гидроцилиндров, трубопроводы гидросистем высокого давления, болты для крепления крыла к фюзеляжу зубчатые передачи редукторов двигателей, шестерни главного редуктора двигательной установки вертолетов и т.д. И это не случайно, поскольку этот, пусть и давно известный материал имеет ряд преимуществ перед своими молодыми "собратьями". Его отличают более высокая жесткость и прочность (что особенно проявляется в мелких деталях), сопротивление циклическим нагрузкам, коррозионная стойкость, хорошая технологичность, т.е. возможность получать заготовки и детали самым разным способом - горячей и холодной деформацией, механической обработкой, сваркой, пайкой и т.д. К тому же сталь стоит относительно недорого. Вот почему со дня основания нашего института одной из приоритетных задач стало создание новых разновидностей сталей.
Постоянное совершенствование конструкций летательных аппаратов требовало непрерывного повышения прочности и удельной прочности (отношение прочности к плотности материала) при сохранении всех преимуществ сталей. Если в авиации до 1941 г. первый из этих параметров колебался от 800 до 1000 МПа, то сейчас - от 1300 до 2000. Впрочем, сложность проблемы заключается не столько в достижении таких показателей, сколько в обеспечении работоспособности выполненных из соответствующих материалов авиационных конструкций.
Дело в том, что повышение прочности сталей ведет к снижению их пластичности, вязкости, трещиностойкости и т.д. В связи с этим разработчики новых их разновидностей ведут непрерывный поиск компромиссов между повышением прочности и обеспечением надежности. В настоящее время в авиационной технике чаще всего применяют три группы высокопрочных сталей: конструкционные среднелегированные; коррозионностойкие; используемые для изготовления деталей, работающих в тяжелых условиях с повышенным трением и подвергаемых химико-термической обработке.
Но в любом случае появление таких материалов заставило пересмотреть принятые ранее подходы к конструированию и технологии изготовления деталей, так как все перечисленные стали обладают рядом специфических особенностей и существенно отличаются от созданных ранее и имевших среднюю прочность (до 1400 МПа). В частности, оказалось: нарушение технологического цикла их получения может приводить к преждевременному выходу из строя деталей, несмотря на полную доброкачественность металла. При этом очагами разрушения могут быть поверхностные или подповерхностные дефекты, полученные на различных стадиях изготовления полуфабриката, самой детали или конструкции целиком. Потому-то было очень важно разработать четкие организационно-технические мероприятия, включающие инструкции по термической и механической обработке деталей, защите от коррозии, сварке и т.д., что нами и было сделано в начале 60-х годов XX в. Кроме того, существенно изменился и подход к изделиям из высокопрочных сталей; основными требованиями к ним стали минимальная концентрация напряжений и высокая чистота поверхности.
Итак, новые стали заняли свое место в авиастроении, причем в зависимости от предела прочности из них изготавливают разные детали. Скажем, если этот параметр находится в пределах 1600-1800 МПа, то такой металл пригоден для производства силового набора планера (лонжероны, различные балки, рамы, оси и т.д.). А стали ВКС-8 (1800-2000 МПа) и ВКС-9 (1950-2100 МПа) незаменимы при изготовлении крупногабаритных сварных деталей (возможна электроннолучевая и аргонно-дуговая сварка) планера и шасси в машинах Конструкторских бюро им. Сухого, Антонова, Микояна, Камова. Мало того. Стали с пределом прочности выше 1950 МПа с успехом заменяют титановые сплавы, что позволяет при их одинаковой удельной прочности существенно уменьшить затраты на производство.
В последние десятилетия разработан новый класс высокопрочных, или так называемых мартенситностареющих сталей. Их прочность 1450-2500 МПа, они обладают уникальными физико-механическими и технологическими свойствами. Например, благодаря низкому содержанию углерода и азота имеют высокую пластичность, вязкость, сопротивление повторностатическим нагрузкам и коррозионному растрескиванию. Этот материал очень технологичен, т.е. заготовки, выполненные из него, после закалки можно подвергать различным видам холодной обработки давлением (раскатку обечаек, накатку резьбы и т.д.), без затруднений обрабатывать режущим инструментом, а затем повышать в два раза их прочность простой термической обработкой - старением (нагрев и охлаждение на воздухе) при относительно низких температурах.
Перечисленные преимущества мартенситностареющих сталей наиболее полно реализуются при изготовлении деталей сложной формы с малыми допусками (в том числе и прецизионных), подвергаемых химико-термической обработке . Металл такого класса нашел применение в тяжелонагруженных узлах истребителей МиГ-31 и МиГ-29, деталей узла поворота и шасси орбитального космического корабля многоразового использования "Буран" и др.
Дальнейшее развитие самолетостроения выдвинуло очередные требования к материалам. В первую очередь речь идет об истребителях, скорость которых опережает звук в 2,5-3 раза, так как для этого они должны преодолевать тепловой барьер - температуры в 280-300 о С, когда алюминиевые сплавы неприменимы. Мы сумели решить и эту задачу. Предложенные нами высокопрочные коррозионностойкие стали обладают всеми необходимыми качествами: высокой прочностью, пластичностью, вязкостью, высокими технологическими свойствами - их легко штамповать, сваривать. Последнее свойство позволяет обойтись без дальнейшей термообработки, и в результате можно создавать сложные, ажурные конструкции, скажем, несущие баки-кессоны, причем без помощи герметиков и клепки, ранее широко применяемых.
Основным материалом в цельносварных самолетных отсеках сверхзвуковых самолетов серии Ми Г стала коррозионностойкая сталь ВНС-2 с пределом прочности 1250- 1400 МПа. В виде листа и ленты ее применяют для обшивки и внутреннего набора, а также при изготовлении силовых деталей (прутки, поковки и т.д.).
Однако в процессе эксплуатации летательных аппаратов, в которых была использована сталь ВНС-2, выяснилось: она недостаточно пригодна в условиях влажного климата (скажем, Средиземноморья). Дальнейший поиск позволил нам получить новые стали ЭП817 (пруток) и ВНС-41 (лист). По своим механическим характеристикам и технологичности они соответствуют уже проверенной ВНС-2, а за счет новой системы легирования и оптимизации режима упрочняющего старения значительно превосходят ее по коррозионной стойкости, причем это касается как основных деталей, так и сварных соединений.
Наибольшее распространение из материалов этого класса получила сталь ВНС-5 с пределом прочности 1380-1600 МПа. Из нее изготавливают силовые детали планеров МиГ и Су, а также шасси гидросамолета Конструкторского бюро им. Бериева. Применяют ее и в гражданской авиации (широкофюзеляжный самолет Ил-86 и аэробус Ил-96) - при производстве высоконагруженных болтов для крепления двигателя к фюзеляжу
Еще один представитель этого класса металлов - сталь СН-2А с пределом прочности 1100-1300 МПа. Она прекрасно зарекомендовала себя как материал для силовых, в том числе крепежных деталей, а также воздушных и кислородных баллонов, которыми оснащены все виды самолетов, включая морскую авиацию. Важнейшая особенность таких баллонов - при пулевом поражении они не разлетаются на осколки.
Сейчас в авиационной и ракетной технике все большее распространение находит новый вид топлива - водород и его окислитель - жидкий кислород, имеющий температуру - 253 градуса. Для работы в таких условиях в нашем институте разработали специальные высокопрочные коррозионностойкие стали (ВНС-25, ВНС-49, ВНС-59) с пределом прочности 1000-1400 МПа при комнатной температуре и 1700-2100 при 20 К (-253 градуса). Этот металл успешно применяют в различных жидкостно-ракетных двигателях, в частности, в самом мощном из них в мире марки PD-170 конструкции КБ "Энергомаш". Детали из этого материала - корпуса насосов и регуляторов подачи горючего - составляют 50-60% от их массы.
В качестве конструкционных материалов, а также для изготовления деталей редукторов и агрегатов, подвергаемых химико-термической обработке, ныне широко применяют среднелегированные и коррозионно-стойкие стали. Объясняется это тем, что в результате долгих изысканий удалось предложить технологию, обеспечивающую сочетание необходимых свойств поверхностного слоя изделия (высокие твердость, износостойкость, сопротивление усталости) и его сердцевины (пластичность, вязкость, технологичность и др.). Так, для тяжелонагруженных, крупномодульных шестерен редукторов разработана сталь ВКС-7 с карбонитридным упрочнением, обеспечивающая после химико-термической обработки глубину упрочняющего слоя до 2,5 мм и твердость больше 60 HRC, что обеспечивает высокую контактную выносливость при рабочих температурах до 250С (пока таких аналогов нет).
Отдельный разговор о вертолетах. Для них в нашем институте создана высокопрочная (до 1300 МПа), износостойкая, теплопрочная сталь ВКС-10. В отличие от серийных отечественных и зарубежных аналогов, работающих при температуре до 250 градусов, она выдерживает 450 градусов. Ее применение обеспечивает передачу больших крутящихся моментов, при которых в зоне контакта зубьев происходит локальное повышение температуры, и даже при нарушении подачи масла работа редуктора может продолжаться в течение 2 ч без аварии.
Все вышесказанное свидетельствует: в авиастроении сталь традиционно остается основным материалом, хотя и она, как, впрочем, и другие творения рук человеческих, требует дальнейшего совершенствования.
Сопротивление усталости характеризуется пределом выносливости - наибольшим напряжением, которое может выдержать материал без разрушения при заданном числе циклических воздействий.
Член-корреспондент РАН Е. М. КАБЛОВ, генеральный директор ГНЦ РФ Государственного предприятия "ВИАМ", доктор технических наук А. Ф. ПЕТРАКОВ, главный научный сотрудник того же центра